Introduction
In the realm of industrial operations, particularly in materials handling and processing, conveyor systems play a crucial role in ensuring efficiency and productivity. Among the critical aspects of conveyor belt maintenance and repair is the method chosen to join and repair belts. This paper delves into the comparative analysis of two predominant belt-joining techniques: vulcanization and mechanical fastening. Through a robust examination of each method’s advantages, we aim to provide insights into why vulcanization might be the preferred choice for many applications, considering longevity, strength, smooth operation, and cost-effectiveness.
Understanding the Basics
Vulcanization Overview
Vulcanization is a process of belt repair and joining that involves the use of heat, pressure, and chemicals to create a seamless and strong splice. This method chemically bonds the belt materials together, resulting in a splice that is nearly as strong as the original belt material.
Mechanical Fasteners Overview
Mechanical fastening, on the other hand, involves joining belt ends using metal or plastic fasteners. This method is quick and does not require special equipment or extensive downtime, making it a go-to option for emergency repairs and applications where versatility is needed.
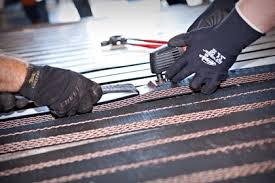
Comparative Analysis
1. Splice Strength and Durability
Vulcanization:
- High Splice Strength: Vulcanized splices achieve near-original belt strength, which can sustain the belt’s tension and load-carrying requirements over time.
- Durability: The chemical bond formed is highly resistant to wear and tear, leading to longer splice life.
Mechanical Fasteners:
- Variable Strength: The strength of mechanically fastened splices depends on the fastener’s quality and installation. They generally do not match the belt’s original strength.
- Potential for Wear: Fasteners can become points of weakness, especially under heavy loads or in the presence of abrasive materials.
2. Operational Smoothness and Efficiency
Vulcanization:
- Seamless Operation: Vulcanized splices create a smooth, seamless surface, minimizing the risk of snagging or catching on conveyor components.
- Energy Efficiency: A smooth splice reduces belt drag and energy consumption, contributing to overall operational efficiency.
Mechanical Fasteners:
- Potential for Snagging: Fasteners may protrude above the belt surface, which can catch on rollers, skirting, and material, leading to damage and inefficiency.
- Increased Energy Demand: The irregular splice surface can increase belt and system drag, raising energy consumption.
3. Application Versatility and Maintenance
Vulcanization:
- Application Specificity: Vulcanization is most effective for fixed systems where belts do not require frequent changes or adjustments.
- Maintenance Needs: While durable, vulcanized splices are more complex to repair or adjust, often requiring specialized equipment and skilled technicians.
Mechanical Fasteners:
- Flexibility: Mechanical splicing allows for quick changes and adjustments, suitable for systems requiring frequent belt modifications or for temporary repairs.
- Ease of Repair: Fastener replacement is straightforward and can be performed in the field with minimal downtime.
4. Cost Considerations
Vulcanization:
- Initial Investment: The upfront costs of vulcanizing equipment and skilled labor are higher compared to mechanical fastening.
- Long-Term Savings: The durability and efficiency of vulcanized splices can lead to lower maintenance costs and energy savings over the belt’s lifespan.
Mechanical Fasteners:
- Lower Initial Cost: Mechanical splicing requires less specialized equipment and training, resulting in lower initial costs.
- Ongoing Maintenance Expenses: Frequent inspections and potential fastener replacements can increase the total cost of ownership.
Conclusion
The choice between vulcanization and mechanical fasteners for conveyor belt repair and joining depends on various factors, including the specific application, operational requirements, and cost considerations. Vulcanization, with its superior splice strength, durability, and operational efficiency, offers significant advantages for permanent, high-tensile conveyor systems. In contrast, mechanical fastening provides flexibility and ease of use for temporary repairs and applications with frequent belt adjustments.
Ultimately, the decision should be based on a comprehensive analysis of the conveyor system’s needs, taking into account the long-term operational and financial impacts. By carefully considering these factors, organizations can select the most appropriate and cost-effective method for maintaining their conveyor belt systems, ensuring their longevity and efficiency.